Fpt industrial‘s ebm 5, the brand’s latest battery management system, has achieved one of the highest levels of certification of industry standards, now offering even greater safety guarantees for customers. The company also took part in Rematec 2025, the world’s leading trade fair for the regeneration sector
Fpt Industrial, alongside its Potenza Technology brand, reaffirms its strong commitment to technological innovation as a tool to continuously improve the products offered to its customers. This constant effort has led to another important milestone: the eBM 5 Battery Management System (BMS) for high voltage batteries, completely designed internally within the company, has obtained the ISO 26262 ASIL C certification as a stand-alone system by TÜV SÜD.
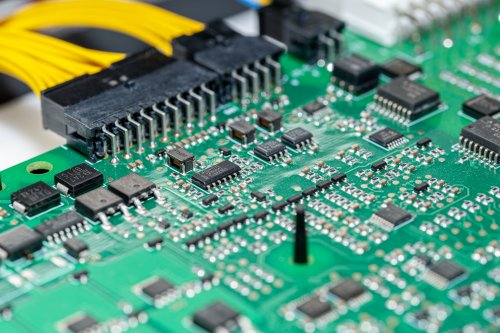
This achievement highlights the qualities of the fifth-generation Battery Management System (BMS), designed and developed entirely in-house by the integrated team of FPT Industrial and Potenza Technology, from the circuitry to the core software and application levels. This cutting-edge system is characterized by flexibility and scalability.
With a highly modular design at its core, it is compatible with 400 or 800 volt battery systems, configurable at application level to optimize vehicle efficiency and performance. This allows Original Equipment Manufacturers (OEMs) to maximize the effectiveness of the system in all fields of mobility – from commercial vehicles to hypercars – with the possibility of managing multiple packs (which is outside the scope of certification) without the need for an additional controller. The EBM 5 is currently in series production for the IVECO eDaily MY24, as well as for numerous other customers.
ISO 26262 is an international standard for automotive functional safety, applied to electrical and electronic systems comprising hardware and software components in vehicles. This standard defines requirements for both the safety functions of the system and the development process, ensuring that an adequate level of safety is maintained throughout the life cycle of the vehicle. The standard is based on the ASIL (Automotive Safety Integrity Level), a risk classification system that analyses potential hazards considering the severity, frequency and controllability of vehicle operating scenarios.
Fpt Industrial protagonist at Rematec 2025
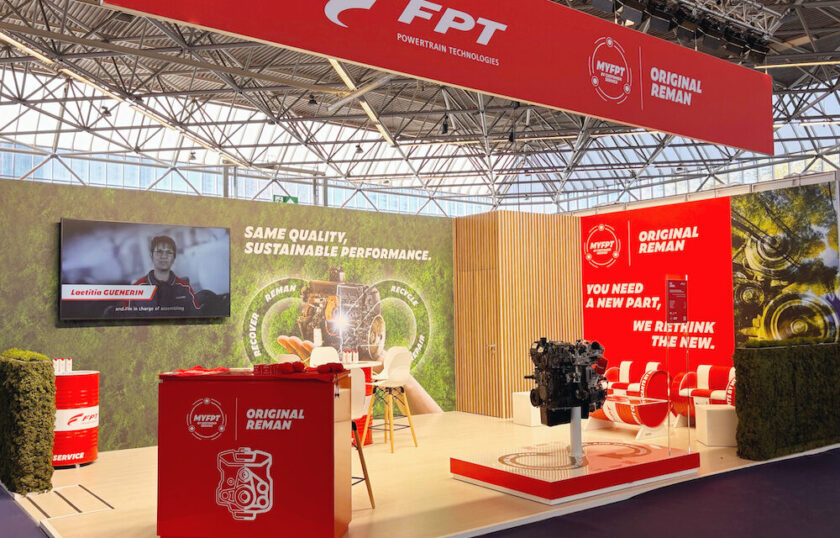
Fpt Industrial showcased its world dedicated to original remanufacturing at Rematec 2025, the world’s leading remanufacturing trade fair for industry professionals, held in Amsterdam (The Netherlands) from 8 to 10 April. Here, the company highlighted its leadership in Original Reman solutions by showcasing its range of original remanufactured engines and components. At the stand, visitors had the opportunity to see a remanufactured F1C engine – the 3-litre Common Rail diesel engine for on-road applications – split in half to show a cross-section that highlights the quality of the Reman product and the remanufacturing process.
Circular economy with Fpt
With the global shift towards a circular economy, remanufacturing has become a cornerstone of sustainable industrial practices, extending the life of vehicle components and significantly reducing waste and emissions. Fpt Industrial fully embraces this approach, integrating sustainability with uncompromising quality and safety.
The company, in particular, boasts a highly advanced remanufacturing process, where each original component is subjected to a rigorous six-step process. First, each component is carefully disassembled and assessed to identify product improvement opportunities during the inspection phase.
Next, specially designed, environmentally friendly cleaning processes are used to ensure thorough cleaning. The components are then subjected to a thorough re-inspection and expert compliance check, followed by a functional analysis in the component certification phase, to meet the required standards. In the remanufacturing phase, components are improved and renewed through mechanical upgrades, product improvements and the integration of new parts when necessary.
Expert reassembly follows, ensuring the highest quality and performance, combining remanufactured components with new parts. Finally, customised 100% load testing is carried out to ensure that the remanufactured components meet the same performance standards as new parts, ensuring their reliability.
Guaranteed reliability and safety
This meticulous process ensures that each part meets the original performance standards, offering the same reliability as new components. Through rigorous quality controls and innovative manufacturing techniques, FPT Industrial Original Reman provides high-performance solutions with a low Total Cost of Ownership (TCO), a two-year warranty and reduced downtime, maximising both efficiency and sustainability.
The remanufacturing process takes place in Garchizy, France, the company’s main Reman centre, alongside its facilities in Turin, Italy. Here, expert teams inspect and restore 12,000 engines and transmissions and 22,000 spare parts annually. Thanks to the recovery of key components, Fpt Industrial Original Reman allows for 80% energy savings compared to new production and prevents the emission of 28 million tons of CO₂ per year – the equivalent of 350 tankers of crude oil, the energy produced by eight nuclear power plants and the amount of gasoline needed for six million cars.
Title: Fpt Industrial: safety, innovation and circular economy
Source: Fpt Industrial